Mid-Coast Corridor Program Delivered with a Project-First Mentality
More than 8,500 people gathered at the University of California San Diego’s Warren Field this past November to celebrate the opening of the Mid-Coast Extension of the UC San Diego Blue Line Trolley. The extension provides a one-seat ride from the U.S./Mexico border to University City and carries with it the promise to increase opportunities for the region’s residents and help the region achieve its climate action goals.
The extension was called “a phenomenal addition to [the region’s] public transit system” and is the centerpiece to one of the area’s largest infrastructure programs that took a dozen years of planning, six years of construction and included enhancements to infrastructure that spanned beyond rail improvements and the 11-mile Trolley extension.
“This project presented many unique technical challenges, including difficult geological conditions, utility conflicts, adjacency to an active railroad and construction in an urbanized environment where impacts to businesses, schools and medical facilities had to be carefully mitigated as part of the design development,” said Vladimir Kanevskiy, engineering technical lead for WSP, which served as the lead environmental and engineering consultant for the program.
The San Diego Association of Governments (SANDAG) used the construction manager/general contractor (CM/GC) delivery method to build the Trolley extension, which is now operated by the San Diego Metropolitan Transit System (MTS).
Mid-Coast Transit Constructors (MCTC), a joint venture of Stacy and Witbeck, Herzog and Skanska, was awarded the CM/GC contract. Eric Meisgeier, deputy project manager at MCTC, notes the sheer number of stakeholders involved in the program required a collaborative work environment if the program was to be delivered on time and on budget.
“There was a lot of collaboration,” said Meisgeier. “At the end of the day, it all came down to the kind of people and the culture that the job had, and we had people willing to solve problems and move the project forward.”
The project-first mentality Meisgeier describes permeated through the program’s 1,000-plus team members and helped MCTC and its partners to safely deliver on a complex program.
Collaboration and Innovation
The scope of the program included 25 track miles of ballasted track, seven track miles of direct fixation track, nine stations, 1.4 million cubic yards of earthwork and 500,000 square feet of walls. Seven of the Trolley extension’s 11 miles were constructed within the busy LOSSAN corridor which hosts 60 freight and passenger trains every day.
Initially, the Mid-Coast Corridor project consisted of the Trolley line extension and two heavy rail double tracking projects. However, additional supplemental projects were bid on and incorporated into the work MCTC was performing for SANDAG because these projects had critical interfaces with the original Mid-Coast project.
Meisgeier points to the Gilman Drive Bridge Project and I-5 Auxiliary Lane as one example of how several separate projects all had critical connections. The Trolley extension crosses I-5 at two locations. At one of these locations, California Department of Transportation (Caltrans) required an auxiliary lane on I-5, while SANDAG and UC San Diego needed a new overcrossing at Gilman Drive to provide a link between the west and east campuses of UC San Diego that was to be located directly under a viaduct for the rail project.
“There was no way [the I-5 auxiliary lane and Gilman Drive Bridge] could be built until after we finished the light rail. We negotiated it and [these projects] were brought into our program,” explained Meisgeier. “At one point, we had three levels of construction going on between the light rail, the Gilman Bridge and then at the I-5 level.”
The supplements added complexity to the administrative side of construction with each requiring its own billing, which MCTC managed to support its subcontractors, and each carried different requirements for small and disadvantaged business goals and reporting. Weekly production meetings and monthly cost meetings helped keep this work in line.
Back in the planning phase, SANDAG recognized the corridor improvements would require an immense amount of coordination, which is why the CM/GC delivery method was selected as it inherently brings collaboration to the design, plans and construction of a project.
During preconstruction, MCTC identified a control point that needed to be relocated for work in the LOSSAN corridor to take place. The control point relocation was part of a long-range plan, but not part of the initial scope of the Mid-Coast Corridor project. MCTC worked with SANDAG and North County Transit District (NCTD) to accelerate plans to relocate the control point, which moved train traffic through the corridor and provided space for the Mid-Coast Corridor project to be constructed.
MCTC also worked closely with NCTD on the Joint Right of Entry (JROE) permits required to work adjacent to an active railroad. MCTC says the process was revised to support a large-scale construction effort. MCTC worked with NCTD to provide delineation for certain work activities to proceed uninterrupted. . In addition to a refined permitting process, MCTC hired supplemental flaggers to help support safe working conditions throughout the corridor.
Working adjacent to active tracks also required innovation when it came to construction elements outside of the tracks, such as retaining walls. The original design called for cast-in-place walls using a soldier pile shoring system and mechanically stabilized earth (MSE) walls. According to MCTC, “geotechnical investigations determined that the top 15 feet of the existing ground was full of large cobbles and caving soils which presented high schedule and cost risk for soldier pile installation. Compounding the problem was that the railroad would not allow MSE walls.”
The solution was a pre-cast retaining wall system, which eliminated the need for shoring through the use of slot cuts where narrow excavations were made along the tracks without compromising the existing embankment. MCTC says the wall system reduced excavation and export of potentially contaminated materials, allowed for rail operations to continue uninterrupted and saved millions of dollars and months of the schedule.
Effective Training
As with all rail projects, safety was paramount, and the project concluded with an admirable safety record. In an industry where the average recordable incident rate is 3.4 and the average lost time incident rate is 1.2, MCTC employees had a 1.28 recordable incident rate and a 0.17 lost time incident rate based on 3.43-million manhours worked. Subcontractors had a 1.27 recordable incident rate and a 0.23 lost time incident rate with 1.73-million manhours worked.
Meisgeier notes the culture of the project was also steeped in safety, which began early in the program with a third-party assessment of the program’s safety culture and climate. MCTC says all levels of management brought the focus on safety to the craft level, giving ownership and accountability for safety to all members of the team. Subcontractors were included in every safety meeting and each one was paired with an MCTC employee who provided mentoring and assistance, as well as performed regular audits on safety performance and compliance.
MCTC provided more than 4,000 Roadway Work Protection training courses for employees in heavy rail and light rail and participated in annual Construction Safety Week activities. MCTC also used “cross-job safety tours” where supervisors from other projects would visit to evaluate safety practices while MCTC employees would do the same. The result was the development of shared best practices.
Meisgeier says one practice gained from these tours was the use of white cones put out by supervisors to indicate where employees could park at the job site. The practice was picked up from a visit to a Seattle, Wash., job site. Meisgeier says it may not seem like a big deal on the surface, but on a transit job site where clearances are tight, it made supervisors think about what and where the work was being performed and brought awareness to the job site.
One of the most unexpected and largest risks to safety was the spread of the COVID-19 pandemic. MCTC worked to get ahead of procuring PPE for its teams, modified the way briefings were conducted, staggered crew start times and tried to minimize the number of high touch items, like taking verbal role call versus using a sign-in clipboard.
MCTC’s training efforts extended beyond job safety. The joint venture provided more than 4,500 individual environmental orientation trainings, required anti-harassment training of managers and initiated a program called Working Minds: Suicide Prevention in the Workplace.
“Construction has the highest rate of suicides out of any industry,” explained Meisgeier. “There is a stigma and we started looking at what common threads exist: long hours, sometimes working nights, isolation from your family. We had a connection to someone who was doing similar training for the military and who was willing to speak to our team. It evolved and we found the Working Minds Program, which works to build suicide awareness. Our goal was to get rid of the stigma and to let people know there are resources available. We also wanted to bring a comfort level and the training needed to talk to people to try to understand who may need help. And a big part of this is letting someone know in the right moment that someone cares about them.”
In addition to the safety, environmental and mental health training that occurred on the project, SANDAG and MCTC were dedicated to the advancement and success of small and disadvantaged firms. These efforts began with procurements and a subcontracting plan MCTC says balanced “custom subcontract packaging, outreach, marketing and mentoring.”
SANDAG and MCTC worked together to exceed project goals for utilizing small and disadvantaged firms, enabling several companies to grow their workforces and secure additional contracts. MCTC published a regular DBE Connection newsletter that shared participation statistics, construction updates, as well as procurement and mentorship opportunities. MCTC staff mentored four DBE subcontractors through a formal program, in addition to the informal mentoring efforts. Through MCTC’s commitment to supporting small and DBE firms, the project was recognized by the Small Business Administration as Minority Small Business Champion of the Year. Additionally, the Federal Highway Administration used the project as an example to develop best practices for DBE programs.
Gauging Success
Measuring how much the Mid-Coast Corridor program accomplished can be done in several ways. The program’s central project, the Mid-Coast Extension of the UC San Diego Blue Line Trolley, was one of only three rail transit projects in the United States to open for service in 2021. Its impact could be seen immediately. San Diego MTS reported ridership on its Trolley system increased 74 percent on the extension’s opening day compared to the week prior.
“When we began this project, we knew it would be a game-changer for our region. This line had been under construction for five years, and the excitement and anticipation we all had at MTS was equally matched by the community,” said Sharon Cooney, MTS chief executive officer. “The new Trolley extension expanded our system by 20 percent and is already opening opportunities to connect thousands of community members to healthcare, education and new jobs.”
MCTC was also recognized by the National Railroad Construction and Maintenance Association with its 2021 Large Project of the Year, which honors “innovation, expertise and quality project management applied towards the successful execution of a rail construction project.”
In a letter supporting the MCTC’s nomination as Large Project of the Year, Jim Starling, construction program manager at Jacobs and construction manager representative for SANDAG, called the final product “a highly successful project” that exceeded expectations “for partnership, collaboration, performance, schedule achievement and issue resolution.”
For Meisgeier, it comes back to a team of people working toward a common goal.
“Everybody who has seen this project says how it went amazingly well, but there were no fewer issues on this job than any other mega project. There were some really tough issues, but the key was the collaboration and the project first mentality of the team members,” said Meisgeier. “I’ve heard [it] said that this was like a family. You might disagree with them, but you’re looking out for them at the end of the day. Everybody [on this project] checked their egos and put the project first and, to me, that’s the greatest story out of this project.”
By the numbers
- 25 track-miles of ballast track;
- 7 track-miles of direct fixation track;
- 21 heavy rail, light rail and roadway bridges;
- 9 major aerial and at-grade stations;
- 1 parking garage;
- 1 arched roadway bridge over 1-5;
- 1.4 cubic yards of earthwork;
- 500,000 square feet of walls and
- A two-mile bikeway path
Companies involved in the Mid-Coast Corridor Projects:
- Lead Engineer: WSP, HDR and Kleinfelder/Simon Wong
- Program management consultant (PMC): T.Y. Lin International in partnership with HDR
- Construction management: Jacobs Engineering and PGH Wong
- Major Subcontractors: Modern Railway Systems; McCarthy Building Companies; Lucas Builders; SRK Engineering
- Major Suppliers: Oldcastle Infrastructure; L.B. Foster Company; voestalpine Nortrak; Roberson’s Ready-Mix
About the Author
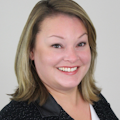
Mischa Wanek-Libman
Group Editorial Director
Mischa Wanek-Libman is director of communications with Transdev North America. She has more than 20 years of experience working in the transportation industry covering construction projects, engineering challenges, transit and rail operations and best practices.
Wanek-Libman has held top editorial positions at freight rail and public transportation business-to-business publications including as editor-in-chief and editorial director of Mass Transit from 2018-2024. She has been recognized for editorial excellence through her individual work, as well as for collaborative content.
She is an active member of the American Public Transportation Association's Marketing and Communications Committee and served 14 years as a Board Observer on the National Railroad Construction and Maintenance Association (NRC) Board of Directors.
She is a graduate of Drake University in Des Moines, Iowa, where she earned a Bachelor of Arts degree in Journalism and Mass Communication.