Safety for any situation
Maintaining transit rail systems can be a complex task and one that can be impacted by the type of environment in which it occurs, the time of day and if nearby track is to remain active. While nothing can replace a robust safety culture and standard safety procedures, there are systems available that can enhance safety of maintenance-of-way crews. These systems leverage technology to provide safety plans with additional layers of protection.
Proactive solutions
Metrom Rail supplies the AURA Train Control System, a full suite of modular solutions that incorporates train control, worker protection and collision avoidance. The system is based on Ultra Wideband (UWB) radio frequency technology, which the company explains allows for highly accurate ranging data and communication capabilities between trains, wayside interfaces, maintenance-of-way equipment and workers. Metrom Rail explains the accuracy of its UWB-based solution is advantageous in underground and urban locations or in other environments where traditional RF-based systems experience difficulty.
“Ranging accuracy and absolute distance measurement is vital to enforcing a reliable and consistent safety system,” said Rick Carlson, Jr., director, business development and corporate strategy. “As AURA can identify the exact distance and speed between two objects, it can then identify the exact point where action must be taken to maintain safe operating behavior. In other words, AURA serves as a proactive tool for safety, as opposed to one that only works when operating rules have been violated.”
Metrom Rail was established in 2010 with a goal of creating a new approach to safety and efficiency in both the freight and transit rail sectors. Carlson explains that the complicated relationship between safety and technology means there is a certain amount of trepidation surrounding anything labeled “new”.
“Systems that promise to offer safety must work 100 percent of the time in order to avoid creating a skeptical user base that might not trust or even use the systems as indicated. Looking past this, it can be difficult to reconcile the theoretical versus practical benefits of technologies,” said Carlson. “Additionally, it is no secret that this industry does not historically welcome or adopt new technologies with open arms. We are encouraged to see an accelerating trend in transit agencies embracing new ideas and concepts and we hope to maintain a role in further modernizing the industry.”
Carlson says UWB technology is shaping the way Metrom Rail reimagines the concept of safety and its application in the AURA Train Control System allows for the safe operation of trains through work zones, to communicate and maintain safe distances to MOW equipment and to each other.
AURA Collision Avoidance Systems can identify the distance and closure rate between trains or MOW equipment. The systems will provide advanced warning that action must be taken to maintain a programmed separation distance and will automatically apply brakes to enforce the distance.
“As this system operates with speed in mind, distances can be configured – for example, an agency may choose to stop trains above 20 mph at 200 feet and trains under 5 mph at five feet to facilitate double berthing or slow operation between MOW equipment,” said Carlson. “The concept of interoperability between MOW equipment and trains has always been a difficult thing to overcome for traditional systems; AURA addresses this to allow maintenance and revenue service to operate in parallel as efficiently as possible.”
Referencing his earlier comment about the complicated relationship between safety and technology, Carlson points to the AURA Worker Protection System (WPS) as an example of the changing dynamic between safety and technology.
“Before the WPS, agencies relied on training and operational standards to protect on-track workers; this was largely due to a lack of systems that could practically support a sensible worker protection plan, notwithstanding enforcement of [positive train control (PTC)] worker protection requirements. The AURA WPS introduces work zones, inside of which workers wearing vests equipped with UWB technology are alerted to an oncoming train. This alarm is customized to each agency, but as a baseline, our requirements for validation of the system were 15 seconds of advanced warning at 60 mph. Both the workers and train operator receive alarms, which require confirmation by pressing a single button. Failure to confirm the alarms will cause the train to apply brakes before the work zone, coming to a stop prior to violating the defined zone,” he said.
Carlson explains that Metrom Rail will continue to explore ways UWB can be applied to enhance safety within the rail industry from how UWB-based technology can address longstanding Positive Train Control interoperability challenges to how the technology can meet property trespassing and platform fall detection needs.
“Metrom Rail is focused on innovative, sometimes unorthodox uses of UWB technology to solve industry problems. We’re excited to continue pushing the envelope on UWB applications to shape modern transit technology approaches,” said Carlson.
Additional level of safety
Miller Ingenuity’s ZoneGuard is an electronic roadway worker protection system (eRWP) that is engineered to work in tandem with standard rail safety procedures. The system warns rail maintenance crews of incoming track vehicles within their work zones with an audible and physical alert to each worker’s wearable device. Miller Ingenuity reiterates the system is not meant to replace standard procedures, but to provide an additional level of safety while performing maintenance work.
This eRWP safety solution can be installed affixed to permanent structures, such as a catenary pole, or transported to each jobsite using Miller’s compact and lightweight portable unit.
“ZoneGuard’s flexibility allows it to perform within high-noise urban environments, under high power lines, on bridges, within tunnels and across multiple tracks giving maintenance crews the ability to provide safer work zones wherever they need to operate,” said Miller Ingenuity.
The system’s optional onboard unit is installed within the locomotive cab and can give train operators a warning alert when they are approaching an active work zone. While the onboard unit is not required for the whole ZoneGuard system to operate, the company says that it does provide another level of communication and safety for rail maintenance crews.
Miller Ingenuity notes that many manufacturing and industrial industries, including rail, have been hesitant to evolve themselves from strictly mechanical products to innovative high-tech solutions that would advance their industry. The company says technology is providing the push needed to move the rail industry into innovative territory.
“With the development of rail safety technology, such as PTC or electronic roadway worker protection systems, railroads are able to feel more confident in their ability to provide safer working environments for their employees,” said the company. “Technology is fluid and always evolving, which results in newer and more advanced solutions constantly being developed. ZoneGuard’s patented detection technology is so accurate and unique, that the technology can evolve to many new industry uses over time.”
Miller explains that traditional rail maintenance safety procedures rely on watchman lookouts to warn their crews of track vehicles entering an active work zone.
“This process is incredibly vulnerable to mistakes due to basic human error factors that include distractions, complacency, miscommunication with train operators and inexperience. Seeing the need for technological advancement in this area, Miller developed ZoneGuard to provide rail maintenance crews with the ability to put the responsibility of safety back into their own hands,” said the company.
Miller Ingenuity explains that the ZoneGuard technology can be applied to additional industry needs such as pedestrian and trespasser detection, PTC integration, train performance tracking through the system’s web dashboard and more.
Providing an extra “eye”
Protran Technology, a Harsco Rail Company, offers a suite of safety products for rail maintenance including solutions for roadway worker protection (RWP), collision avoidance for rail maintenance machines and wayside power monitoring.
The company notes that its RWP systems fit a variety of scenarios for fixed and mobile work crews regardless of the physical characteristics of the transit or railroad. These systems can be portable, vehicle or wayside based. Protran Technology explains the systems include advanced train approach warning technology that alerts workers of approaching trains or maintenance vehicles and notifies operators of these vehicles when they are approaching crews on the roadway so they can be aware and, if needed, make appropriate operational adjustments.
Protran Technology says distances for alerts and alarming in its collision avoidance system can be configured for any requirement to provide advanced warning to maintenance vehicle operators in the event another vehicle gets too close during travel or work modes.
The company also offers electrical monitoring and power verification technology for both third rail and catenary systems. This technology allows workers to validate power status and to continually monitor the status of the electrical power system during any rail maintenance activity.
Protran Technology explains that roadway workers and operators no longer have to be placed in unsafe conditions due to potential single point failures in safety and operating rules.
“With the implementation of advanced warning technologies and monitoring equipment, worker safety is now protected by secondary systems in the event primary rules and procedures are violated or those providing primary protection (i.e. flagmen/watchmen) become distracted. Additionally, as operators are tasked with more and more responsibilities collision avoidance technology can add an additional ‘eye’ to assist operators while in work or traveling operations,” said the company. “In Protran’s history at agencies where this technology has been implemented, there have been no railroad worker fatalities and ‘near miss’ occurrences have been reduced to almost zero.”
Protran has worked to enhance safety is in the control center where there may be an inability to pinpoint exact locations of maintenance workers near active tracks.
The company says its recently developed Enhanced Employee Protection System (EEPS) and ProAccess RWP System are tools that now allow transit agencies to track the exact location of multiple crews (both mobile and fixed) while on the roadway.
“These systems allow controllers and managers to gather a tremendous amount of both safety data and track access efficiency data while adding enhanced safety to workers on the trackway. In addition to those current features, we are developing accurate location detection for both assets and rail defects along the trackway,” said Protran. “Having accurate defect location data improves track maintenance efficiency which leads to safer railroads and also improves the time track workers are out on the trackway.”
About the Author
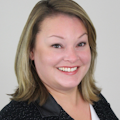
Mischa Wanek-Libman
Group Editorial Director
Mischa Wanek-Libman is director of communications with Transdev North America. She has more than 20 years of experience working in the transportation industry covering construction projects, engineering challenges, transit and rail operations and best practices.
Wanek-Libman has held top editorial positions at freight rail and public transportation business-to-business publications including as editor-in-chief and editorial director of Mass Transit from 2018-2024. She has been recognized for editorial excellence through her individual work, as well as for collaborative content.
She is an active member of the American Public Transportation Association's Marketing and Communications Committee and served 14 years as a Board Observer on the National Railroad Construction and Maintenance Association (NRC) Board of Directors.
She is a graduate of Drake University in Des Moines, Iowa, where she earned a Bachelor of Arts degree in Journalism and Mass Communication.