No Longer Out of Service: Asset Performance Management for the Transportation Industry
With a structured APM program, operators can better predict asset failure and coordinate the necessary repairs through a digital system that manages all maintenance and logistics data to provide actionable recommendations and keep operations running.
In the U.S., insufficient funding combined with poor asset management practices have contributed to an estimated $85.9 billion transit backlog — the reinvestment costs required to replace aging and damaged transportation assets. To make matters worse, the Federal Transit Administration (FTA) estimates that an additional $2.5 billion per year is needed just to prevent this backlog from growing.
Transit systems across North America are aging and are facing rising maintenance costs and increasing pressures from stakeholders to increase service availability while minimizing safety risks. Keeping buses, metro rails and trains running with minimal failure is a tall order given the average age of their equipment and infrastructures. Doing so without an effective asset performance management (APM) system to monitor performance, provide critical operational insight, increase reliability and creation of asset strategies, predict failure and give management strategic recommendations is a near impossibility.
To jumpstart an APM initiative, the FTA is developing standards for APM initiatives. These standards will serve as a guide for organizations as they implement technologies and programs to help sustain their transportation assets and enable staff and executives to develop intelligent strategies to manage their assets and infrastructure.
Traditional techniques for enterprise asset management (EAM), such as manual data collection, limited analytics, and simple, non-differentiating maintenance strategies are no longer sufficient in our data-driven world. These outdated methodologies are putting a strain on the economy. Public rail systems in the U.S. have been plagued by accidents over the past few years, including one in early 2015 where six people were killed after a commuter train struck a Jeep in New York. For public transit systems (and also freight rail), new monitoring, maintenance and management methods are needed to deliver value in the short term and maintain reliability in the long term.
The first part of a robust APM program is to ensure that up-to-date information about assets is available by installing sensors and advanced condition monitoring systems to drive data into APM programs where it can be analyzed and turned into actionable information. Without accurate data, operators are unable to draw conclusions about asset conditions and availability. Further, to make real-time decisions and keep trains running efficiently, operators need to be fully aware of the asset’s condition and any near-term maintenance needs.
Consider this example using an APM program. A light rail vehicle (LRV) is scheduled for a 90-day inspection, and it is three weeks out from its arrival at the shop. An asset-specific performance report for that LRV has been triggered by the EAM system due to repeated failures with the HVAC and automated door systems. The report shows that maintenance expenditures year-to-date are out of control when compared to the fleet average in both parts and labor.
The asset registry for the entire fleet is used to quickly identify a spare LRV for replacement while the existing LRV goes into the shop for early maintenance. The asset registry includes a data historian for each car, which provides a condition status for the spare LRV, allowing the supervisor to easily identify the maintenance and service actions that must be taken to return the spare to service. That work is packaged into a work order (WO) by the supervisor, which he sends to the spares facility and books it into their online schedule; he receives confirmation the WO has been planned and accepted.
Before the LRV can be brought in for service, a wireless condition monitoring system is collecting data on the LRV on the wheels, gear box, bearings, and propulsion system and feeding a predictive maintenance (PdM) tool at a centralized command center. Without warning, an action alert is generated by the PdM tool that forecasts an impending failure. Vibration data suggests that wheel bearing degradation is occurring on the LRV and an impending failure is highly likely in the next 3-5 days. Additionally, the crew submitted a work order request for the doors and HVAC at their last stop, which are malfunctioning.
The management team convenes to review the APM system data and recommendations and determine the optimized maintenance response to this situation. A terminal with a repair bay that can accommodate the LRV is identified, and three work packages are developed and submitted: wheel bearing replacement; HVAC system repair; and door system repair.
Further, as part of an APM initiative, an effective asset safety program provides comprehensive analytics that scrutinize rolling stock, locomotive and infrastructure failures and failure rates, so the data can be used in the design of safety instrumented systems. With APM, the lifecycle of the safety instrumented functions can be managed and designed to be both safe and reliable, thereby reducing asset failures, increasing process safety, controlling costs and even increasing production availability.
It is not enough to simply monitor asset health. Mismanaged aging transportation assets are not only a huge cost burden, they are also an enormous and very real safety concern for the public. The FTA is proposing to amend chapter 49 of the Code of Federal Regulations by adding a new part 625, which will help asset owners reduce risks and costs through the implementation of APM programs. Through better data and planning integration, organizations will more efficiently respond to pending asset failures and increase the reliability of their existing fleet, thereby ensuring safe and reliable operations.
Jim Goldsmith is a transportation account executive with Meridium.
About the Author
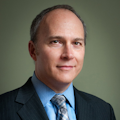