When it comes to developing best practices for handling fleet maintenance, transit managers have been using data to try and keep on top of repairs and routine maintenance.
But as maintenance departments evaluate their practices, some experts are urging them to think beyond maintenance data and expand their scope into data from all aspects of operations.
“A lot of contributions to maintenance needs are due to inefficient operations,” said Niranjan Umarane, senior director, product management for Icertis. “There needs to be a very holistic way of looking at things in terms of how the costs of fleet maintenance are concerned.”
Umarane conducted a Webinar Feb. 5 on the usage of cloud software to handle fleet maintenance costs, where he said such technology can allow managers to lower their maintenance costs and improve operations costs by keeping on top of upkeep of a fleet. He said cloud technology can improve these operations because it allows operators to focus on their mission as opposed to having to manage an IT department just to handle the data coming in or to pay for equipment to store the data.
Using cloud software can also bring in multiple lines of data on fleet vehicles and their routes in to get a better idea of what’s needed for each bus. It allows for managers to discover inefficient routes that are causing maintenance issues or increased tire and fuel costs, along with driver habits that are also pushing these expenses higher.
Data can come from multiple sources, including riders using social media, who provide an extra set of eyes on the fleet and then report an issue.
It also allows a maintenance department to fully customize its service to the fleet because the data provides a much more accurate account of when to take preventative maintenance measures as opposed to following OEM spec, which are written in broader terms. Using driver habits, idle time, route data, climate the fleet runs in and other data can allow maintenance managers to get a better prediction on when a part will fail.
“Fifty percent of fuel escalations for an operation happen because of inefficient routing or scheduling,” he said. “It has nothing to do with maintenance; it has nothing to do with driving habits.”
In addition to keeping an eye on how a fleet is performing, Umarane said integrating outside data with maintenance can allow for a more efficient department. Buses can be scheduled to be used on the proper bays depending on the services needed, work order histories allow for managers to follow trends with a particular bus or part and it also allows them to track which technicians are working on the buses and if any complaints have been filed by drivers.
It also allows for more efficient procurement processes, Umarane said, because pooling data in a cloud format can show if a particular part is failing often and when replacements need to be purchased.
“On the serviceability side, it’s all about productivity. What’s the turnaround time, response time to a breakdown,” he said.
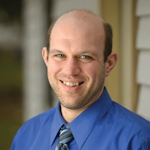
Joe Petrie | Associate Editor
I came to Mass Transit in 2013 after spending seven years on the daily newsbeat in southeastern Wisconsin.
Based in Milwaukee, I worked as a daily newspaper reporter with the Waukesha Freeman from 2006-2011, where I covered education, county and state government. I went on to cover courts for Patch.com, where I was the main courts reporter in the Metro Milwaukee cluster of websites.
I’ve won multiple awards during the course of my career and have covered some of the biggest political events in the past decade and have appeared on national programs.
Having covered local government and social issues, I discovered the importance of transit and the impact it can have on communities when implemented, supported and funded.